Metal plating – time for a bath!
The two most common ways to deposit metal on a surface are electroplating or electroless plating. Both methods have their pros and cons, but they all start with a substrate taking a bath. Here is a brief overview of the two methods.
Electroplating, as the name suggests, involves an electric current. It utilizes the process of electrolysis, where you have an anode connected to a cathode in an electrolyte solution. The anode consists of the element which you want to deposit on your cathode. The anode can typically be made of nickel or copper. If an electric current is placed between the anode and the cathode, the current will cause the metal atoms of the anode to deposit onto the surface of the cathode and thus creating a metal deposit of the anode metal. Since this technique involves an electric current, your cathode needs to be made of a conductive material. Your electrolyte should also include the metal which you are to deposit on the cathode.
In electroless plating, as the name suggests, you do not use an electric current to plate your surface. This means that the object you want to deposit your metal on does not need to have conductive properties. It utilizes an autocatalytic process which only involes chemical reactions. By chemically interfere with the substrate surface, you bind your metal ions to your substrate surface. In electroless plating you need a bath with metal salt (e.g. a nickel salt), a reducing agent and a stabilizer. The reducing agent in the bath reduces the metal ions of the salt, creating elemental metal which is deposited on the surface.
At W&F, we offer several chemicals used both for electroplating and electroless plating. We offer a wide range of metal salts, and we also have sodium hypophosphite monohydrate (SHP) in stock, which is a very common reducing agent for electroless plating.
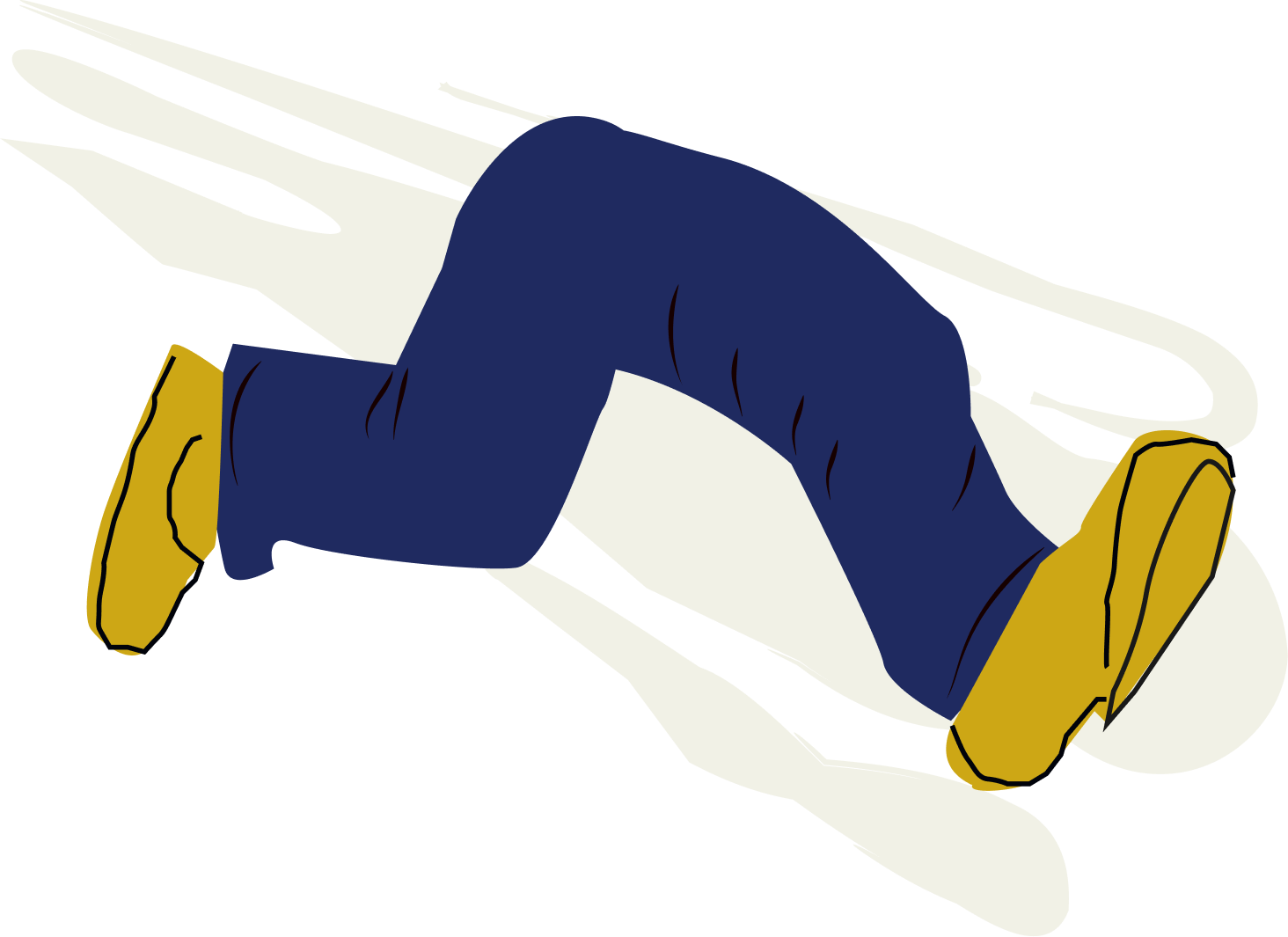